1. What is ICT?
ICT (In-Circuit Test) is a type of test used in PCBA (Printed Circuit Board Assembly) manufacturing to detect faults and defects in the assembly process. It involves using a dedicated test fixture to probe the electrical components on the PCB, and performing a series of automated tests to verify their correct operation. ICT is typically used to test the functionality of components such as resistors, capacitors, and integrated circuits, and to check for open circuits, short circuits, and other common faults. ICT is a valuable tool for ensuring the quality and reliability of PCBA products, and is often used in combination with other testing methods such as functional testing and X-ray inspection.
2. ICT Types
ICT testing generally has two types, offline (Off-Line) and online (In-Line), depending on the production mode. Typically, ICT requires customized test fixtures based on product size and the position of electronic components. In order to meet the short lead time and flexible production capacity of sample production, flying probe testers (which have the advantage of not requiring test fixtures) are also used, and their test probes can be programmatically moved. However, due to the slow speed of testing time and new program development, they are usually used for sample production testing, while the use of ICT for mass production can maximize productivity.
3. ICT Function.
ICT is like a powerful multimeter that can effectively isolate and test electronic components on a circuit board, which a multimeter cannot do.
ICT is a static test (no power on), which can test and determine the specifications, short circuits, and open circuits of common electronic components such as resistors, capacitors, inductors, diodes, and transistors, using various testing technologies from different manufacturers. In addition, it can also perform data programming for ICs during the testing process.
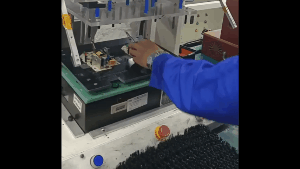
4. ICT Application
ICT is used in the back end of the SMT process, usually behind the SMT line (after the reflow soldering process). The ICT test can screen out defects in the SMT process and provide an early warning of abnormal SMT production yields.
Since ICT needs to test electronic components at different locations on the circuit board, corresponding ICT test fixtures must be made for different products. Test fixtures come in different brands and models, including vacuum and pneumatic types, and require probes of different sizes, shapes, and diameters to contact the circuit board or electronic components. Therefore, if the density of electronic components on the circuit board is too high and there is no space to place probes, ICT may not be used, so there are still limitations to the use of ICT.
5. ICT Test Fixture Stress Test
Due to the differences in the number and distribution of electronic components in different electronic products, the number and density of probes in ICT test fixtures also vary. When the probes contact the circuit board for testing, it may generate pressure (stress) that exceeds the allowable range of the circuit board, causing deformation of the circuit board, which may lead to potential damage to the circuit board product. Therefore, before introducing the ICT test fixture, it is usually necessary to conduct a stress-strain test to reduce the strain value to a safe range that is allowed.
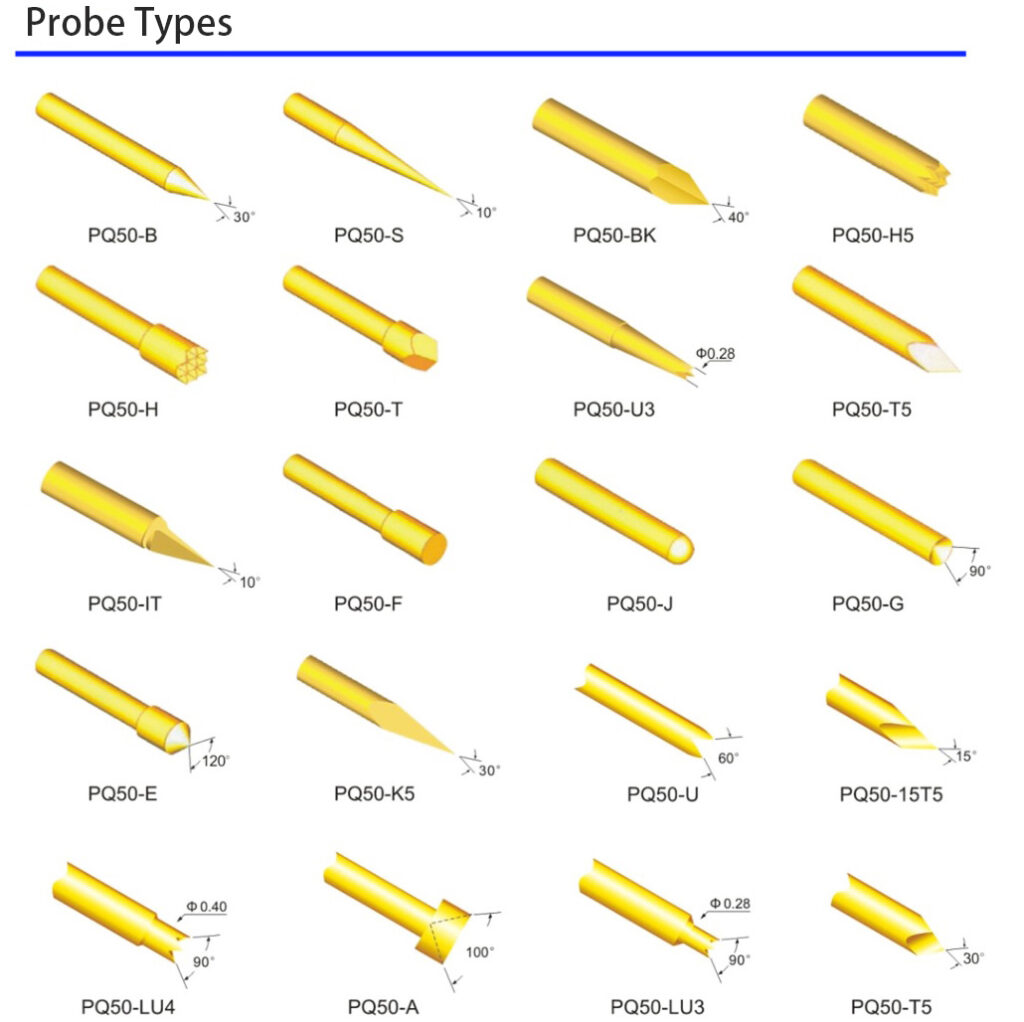
6. Advantages of using ICT to test circuit boards:
▪ Fast testing speed and short testing time. PCBA does not need to be powered on to perform L/C/R/D testing, which can effectively reduce the waiting time for testing startup and lower the risk of circuit board burning accidents caused by short circuits. For a circuit board with 300 components, the testing time can be shortened to 3-5 seconds.
▪ Good repeatability. Controlled by computer programs and precisely measured, it greatly reduces the risk of misjudgment and missed testing, and reduces the troubles on the production line. (However, if there is poor contact at the test point, it may cause misjudgment.)
▪ Low dependence on on-site technicians. Almost the entire process is controlled by a computer, greatly reducing the time and errors caused by human operations. General operators only need a little training to operate the equipment easily and replace testing fixtures on their own. (Test programs must be maintained by professional technicians or engineers.)
▪ Significant reduction in product repair costs. General operators can handle product maintenance work, effectively reducing personnel costs. ICT can inform technicians or engineers which component or Net has problems through computer programs, greatly reducing the speed of retesting and debugging defective products.
▪ Increase product throughput. By quickly testing and giving feedback to the front-end SMT operation, it reduces the defect rate of production, which can reduce material inventory and defective products accumulation, and even lower costs and improve competitiveness.
▪ Improve product quality. As long as there are enough testing points, ICT can measure all the circuits and components on the circuit board, even the components on the bypass line, which can improve product quality, reduce customer complaints, and even improve business performance.
7. Disadvantages of ICT circuit board testing:
▪ The equipment and fixtures for ICT are generally very expensive, especially the pneumatic steel fixtures, which can cost up to NT$400,000 to NT$500,000, making it more suitable for products that are produced in large quantities.
▪ When using ICT testing, additional test points (Test Points) need to be designed on the circuit board for connection with the probe bed, which reduces the utilization rate of the circuit board wiring.
▪ The test points sometimes have contact problems due to different surface treatment methods. For example, OSP boards require solder paste to be added to the test points to achieve contact conductivity, but the flux in the solder paste can form a protective film, resulting in poor contact.
▪ The probe bed needs to be regularly maintained and the probes need to be replaced periodically to ensure their normal operation.