In modern electronic devices, control boards are the core components responsible for implementing complex functionalities, and relays are indispensable elements within these boards. A relay’s function goes beyond merely acting as a switch; it plays a critical role in ensuring the stable operation of equipment. This article, written from the perspective of a control board assembly engineer, provides an in-depth discussion of the fundamental principles, selection criteria, installation layout, testing, and maintenance of relays, giving readers a comprehensive understanding of their application in control boards. Today, we will focus on the latest technologies, development trends, safety aspects, and regulatory requirements related to relays in control board design and manufacturing.
1. New Technologies and Trends in Relays
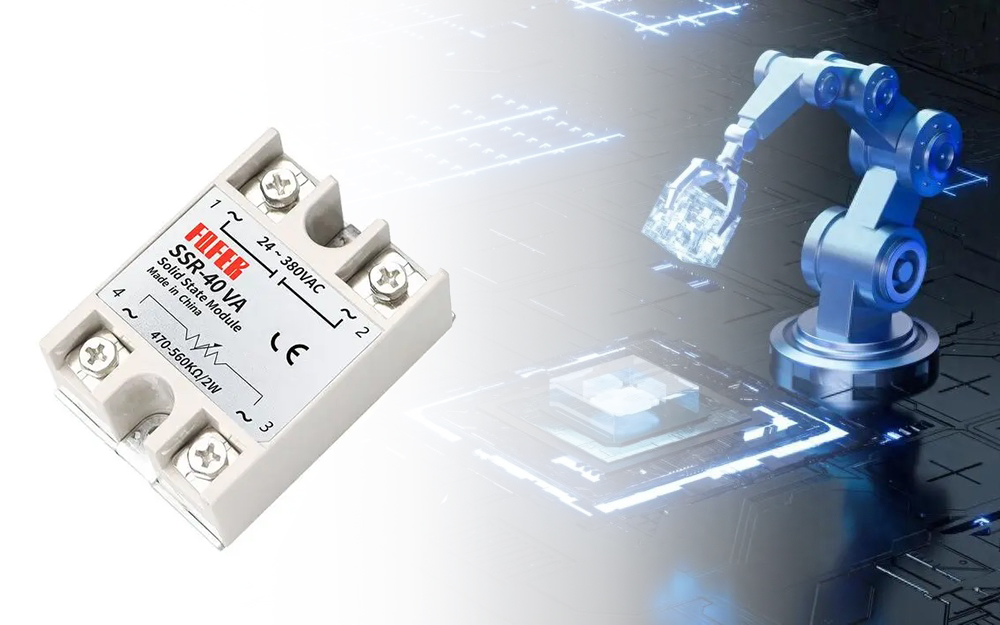
New Materials and Design Advances
- Application of Advanced Materials:
- High-performance Polymers: The development of material sciences has led to the increasing use of high-performance polymers, such as Liquid Crystal Polymers (LCP) and Polyaryletherketones (PAEK), in relays. These materials provide excellent heat resistance and electrical insulation, improving the relay’s overall performance and lifespan.
- Nanomaterials: The introduction of nanomaterials, such as nanosilver and carbon nanotubes, enhances the conductivity and oxidation resistance of contacts. This reduces contact resistance and wear, significantly extending the relay’s service life.
- Ceramic Bases: New ceramic materials are increasingly used in relay substrates, enhancing high-temperature resistance and mechanical strength—especially for applications in extreme environments.
- Advanced Design and Manufacturing Techniques:
- Miniaturization: With advanced microfabrication technologies, relay sizes continue to shrink while maintaining or even improving their electrical performance. This allows relays to fit into more compact circuit designs, particularly in mobile devices and miniature electronic products.
- 3D Printing: The use of 3D printing in relay manufacturing enables engineers to quickly produce prototypes for design validation. This significantly shortens the product development cycle and reduces production costs.
Smart Relays
- Key Features of Smart Relays:
- Self-diagnostic Capabilities: Smart relays are equipped with sensors and microprocessors that monitor operating conditions—such as current, voltage, and temperature—in real-time, providing diagnostic functions. In case of abnormalities, these relays can issue alerts or automatically disconnect to prevent fault escalation.
- Remote Control and Monitoring: Smart relays can be monitored and controlled remotely via networks, allowing operators to view the relay status in real-time and adjust control strategies as needed. This greatly enhances system flexibility and management efficiency.
- Adaptive Functionality: Smart relays incorporate algorithms that enable them to adjust operating parameters—such as switching speed and contact pressure—based on load variations. This optimizes performance and extends the relay’s lifespan.
- Development Trends of Smart Relays:
- IoT Integration: As IoT technologies evolve, integrating smart relays with IoT platforms is becoming a trend. This connection facilitates extensive data collection and analysis, providing insights for system optimization.
- Energy Efficiency and Sustainability: Future smart relays will focus on energy-efficient and environmentally friendly designs, minimizing power consumption and using eco-friendly materials to meet stringent global environmental regulations.
- Multifunctional Integration: Smart relays will evolve toward multifunctional integration, incorporating more sensors, communication modules, and control functions to become a more comprehensive part of electrical control units.
With the continuous emergence of new materials and technologies, relays are moving toward smarter, more efficient, and environmentally friendly designs. This not only enhances control board performance but also opens up new possibilities for innovative applications in electronic devices.
2. Safety and Regulations
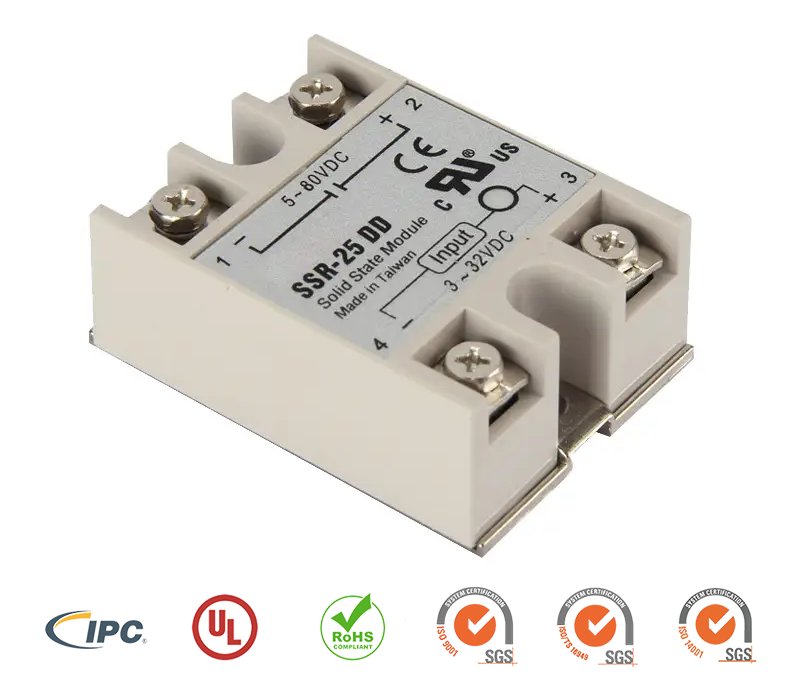
Electrical Safety Standards
- Electrical Safety Considerations:
- Electrical Insulation: Relays must provide adequate electrical insulation to prevent electric shock, including insulation between coils and contacts and between the relay housing and external environments.
- Overcurrent Protection: Proper overcurrent protection mechanisms must be integrated into the design to prevent relay damage or fire hazards caused by excessive currents.
- Thermal Management: Relays should not generate excessive heat during operation. Heat dissipation designs are essential to avoid thermal runaway and ensure safe operation.
- Compliance with International Standards:
- UL Certification (Underwriters Laboratories): Relays intended for the North American market typically require UL certification, ensuring safety under high temperatures, insulation strength, and durability.
- CE Mark (Conformité Européenne): For the European market, relays must meet CE standards, ensuring compliance with EU regulations on safety, health, and environmental protection. CE certification covers electrical safety, electromagnetic compatibility (EMC), and eco-friendliness.
- RoHS Directive: Relays must comply with the EU’s Restriction of Hazardous Substances (RoHS) directive, limiting the use of harmful substances like lead, mercury, and cadmium to ensure product sustainability.
- IEC Standards (International Electrotechnical Commission): IEC standards encompass electrical performance, durability, and environmental adaptability, making them globally recognized technical benchmarks.
Environmental and Reliability Requirements
- Environmental Adaptability:
- Temperature Resistance: Relays must maintain reliability in extreme temperatures, whether in high-temperature industrial equipment or frigid environments. Material selection and design must account for these conditions.
- Humidity and Corrosion Protection: Relays used in humid environments or exposed to corrosive gases must offer excellent sealing and corrosion resistance. Proper sealing structures and corrosion-resistant materials are crucial for long service life.
- Performance Under Harsh Conditions:
- Vibration and Shock Resistance: Relays used in machinery or vehicles must withstand frequent vibrations and shocks to prevent mechanical failure. Engineers must consider installation methods and structural designs to improve mechanical reliability.
- Electromagnetic Interference (EMI) Protection: Relays must maintain stable operation even in high-EMI environments. This can be achieved through shielding designs, filters, or using relays with strong anti-interference capabilities.
By adhering to strict electrical safety standards and ensuring reliability in various environments, the safety of control boards is guaranteed. This not only meets international regulatory requirements but also enhances product reliability and builds customer trust.
Conclusion
In summary, relays play a critical role in the design and manufacturing of control boards. Every stage—from selection and installation to testing and maintenance—affects the performance and reliability of the control board. As technology advances, relays continue to evolve, offering more intelligent and efficient solutions. For control board engineers, mastering relay usage and staying updated on the latest trends not only improves product quality but also extends equipment lifespan, providing customers with superior solutions.