Most of the circuit boards in today’s electronic devices are assembled automatically through reflow soldering, wave soldering, and robotic soldering machines, ensuring efficiency and quality in the soldering process. However, manual soldering methods are still widely employed for the assembly of circuit boards in small-scale prototype devices, soldering special electronic components, and encapsulating extremely small surface-mount components like 0402 or 0201.
1. The Importance of Welding Quality
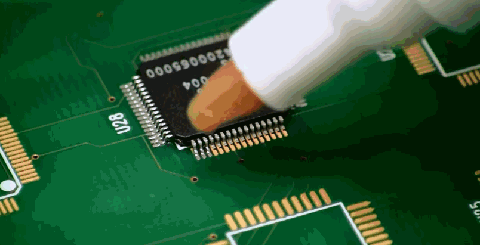
Welding quality is of paramount importance, as it directly impacts the debugging and operation of subsequent equipment. Leaving welding flaws can lead to numerous false readings and make the equipment debugging process difficult, even rendering the equipment inoperable. There are various types of welding errors that can affect the electrical connectivity, mechanical stability, and the occurrence of short circuits and cold solder joints in the solder joints.
To ensure welding quality and minimize potential damage to components on the circuit board during the soldering process, one needs to possess essential soldering knowledge and the necessary hardware. Understanding the principles behind various faults, adhering to soldering standards, cultivating good soldering habits, and developing the ability to observe and assess soldering quality are crucial.
Today, we will discuss some useful techniques and common pitfalls in manual soldering.
2. Manual Soldering Tools
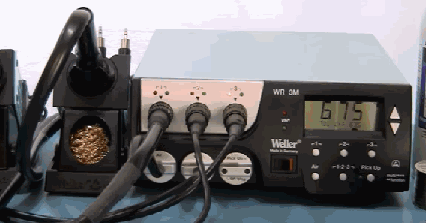
Knowing how to solder and being able to solder well are two different matters. Good soldering tools, coupled with repeated practice, are the fundamental elements for achieving perfect soldering. In modern circuit board design, as components become increasingly densely packed to reduce board size and volume, achieving soldering excellence requires excellence in soldering iron, solder, flux, and soldering processes.
In addition, for devices with pinless packages (such as QFN, BGA, WLCSP, Flip-Chip, etc.), special equipment is needed to complete the soldering process. In specific cases, a hand-held hot air gun can be used to solder devices with fewer pins, which demands proficient soldering skills and rich soldering experience. Otherwise, one could easily fall into the traps of localized high temperatures, electrostatic discharge, or soldering iron leakage.
3. Common Pitfalls in Soldering and Recommended Solutions
Pitfall 1: Chip Deformation Due to Localized High Temperature
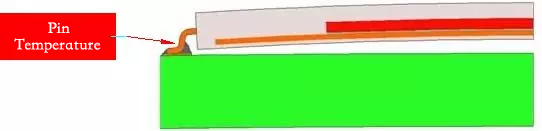
During soldering, there’s a momentary localized high temperature at the chip’s pins. Heat is transferred through the pins into the chip. Different temperature differentials can cause chip deformation, leading to detachment, tearing, or damage to internal wire bonds and the semiconductor substrate, ultimately resulting in chip failure.
Recommended Solution: Reducing the risk of this type of failure revolves around two main points: the temperature of the soldering iron tip and the duration of the soldering process.
To ensure both solder quality and speed, there’s an optimal temperature for the soldering iron tip, depending on the type of solder used. For regular solder with lead (melting point at 183°C), set the soldering iron tip temperature at 315°C. For lead-free solder (melting point at 217°C), set the soldering iron tip temperature at 350°C. Most soldering irons today have automatic temperature controllers to maintain the proper soldering iron tip temperature.
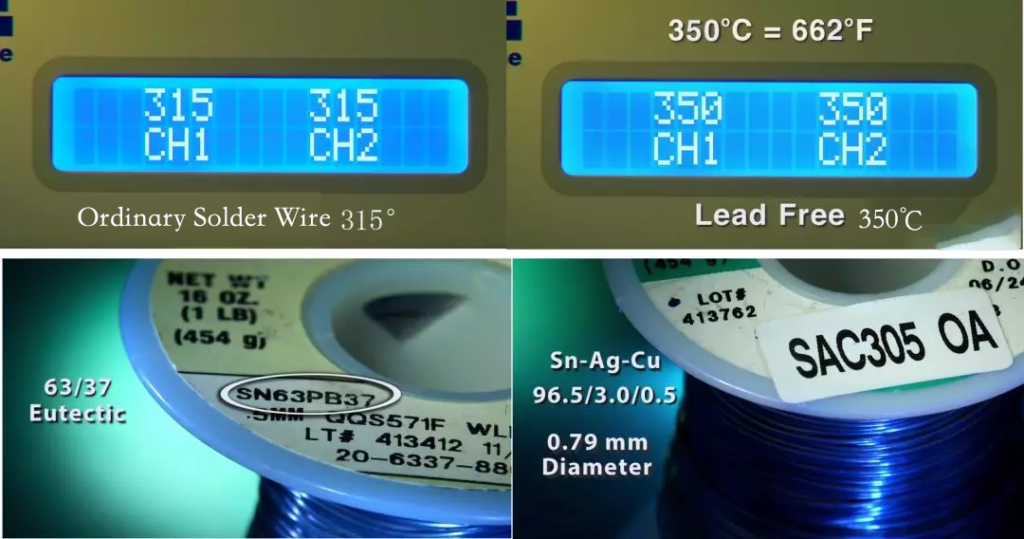
A too-low temperature will result in a longer heating time, reduced solder melting, poor wetting to the pad, and an increased chance of solder bridging. Conversely, a too-high temperature increases the risk of damaging the chip due to excessive heat, and it may also lead to soldering iron tip oxidation and reduced tip lifespan. Soldering duration also affects solder quality and the potential for chip damage. Whenever possible, it’s recommended to keep the soldering duration as short as possible while maintaining solder joint quality.
In cases where the chip has substantial thermal dissipation or there’s a large heat-sinking plane near the solder pads, you can slightly raise the soldering iron tip temperature to ensure proper pad wetting.
Pitfall 2: Human Electrostatic Discharge
Human electrostatic discharge can be a hidden killer of chips. Particularly in dry weather, clothing can generate several thousand to tens of thousands of millijoules of electrostatic charge through friction. This type of electrostatic discharge is a significant risk for semiconductor devices, especially MOS devices, as it can lead to overvoltage breakdown, causing permanent damage or performance degradation.
Recommended Solution: To mitigate the threat of electrostatic discharge to components, attention to the soldering environment is crucial. Place antistatic mats on the soldering work surface and use wooden or cloth-covered chairs to reduce friction-generated static. Wear antistatic wristbands that dissipate electrostatic charges from the body to the ground.
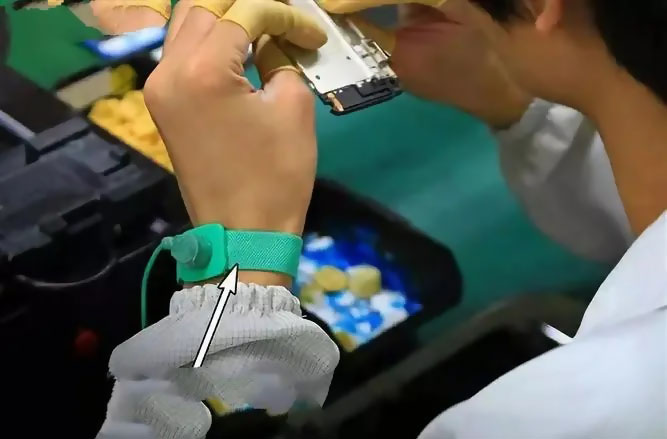
Controlling the humidity of the soldering environment can help discharge any residual static electricity.
Pitfall 3: Soldering Iron Leakage
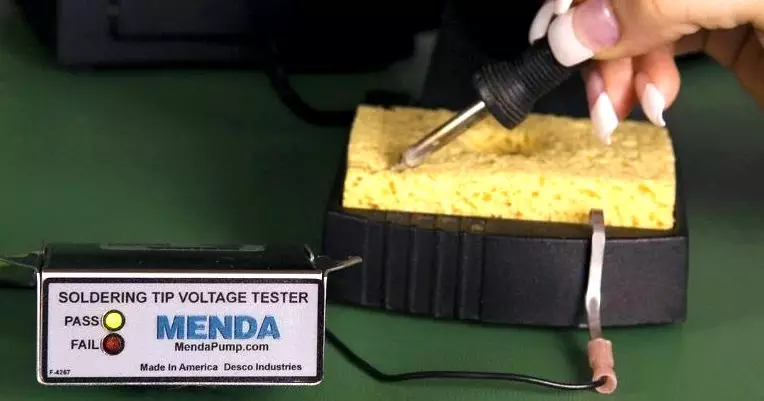
Most soldering irons are powered by standard 220V AC electricity. If a soldering iron is not adequately grounded and has internal leakage due to temperature variations, the metal casing of the soldering iron tip can carry high-voltage AC electricity. For most chips, the AC high voltage exceeds their withstand voltage, leading to chip damage.
Recommended Solution: Soldering equipment usually includes a dedicated grounding wire. Before use, ensure that this wire is adequately connected to a ground. Regularly inspect it using a voltage tester or a specialized soldering iron tip leakage tester to prevent grounding failures and iron leakage.
Additionally, never solder with live equipment. Often during equipment debugging, the power is unintentionally left on. Or the device is switched off, but there may still be residual voltage in the circuit board capacitors. In such cases, soldering could damage the chip.
Therefore, based on the student’s description of the problem, setting the soldering iron tip temperature at around 250°C during soldering is somewhat low, causing solder bridging and resulting in the circuit’s abnormal operation. Additionally, the student did not mention electrostatic discharge control during the soldering process or soldering iron leakage checks, which makes it highly probable that the horrific damage to the IN118 was due to soldering iron leakage.
4. Summary
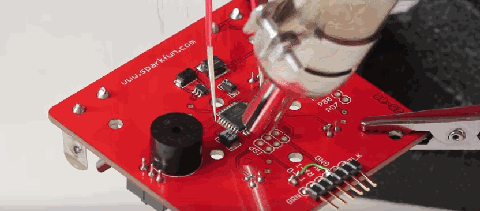
Based on the above analysis, it is unlikely that the soldering iron temperature is the primary cause of chip damage. Another possibility is that the circuit board itself may have defects, preventing the new circuit from functioning correctly. At this point, the explanation for the non-working circuit may have been prematurely attributed to chip damage.
Of course, apart from a slight lack of practical experience, the failure to explore more possibilities for chip soldering damage could be a contributing factor.
Understanding the pitfalls to avoid in hand soldering also requires targeted prevention based on different environmental characteristics. Otherwise, a moment of negligence can result in irreparable losses.
Just as the saying goes, ‘A good tool improves the way you work.’ The same principle applies to the soldering process. High-quality tools not only help solve various soldering challenges but also minimize the risk of damaging the chip.”