Barcode in PCB Production:
A barcode is a graphical representation of data that consists of a series of parallel lines and spaces of varying widths. These codes are typically scanned by optical devices such as barcode scanners or cameras to quickly and accurately read the encoded information. Barcodes are widely used in manufacturing, including PCB production. It could help manufactures to track and manage various aspects of the production process and unleash efficiency.
一、The Functionality of Barcodes in PCB Production:
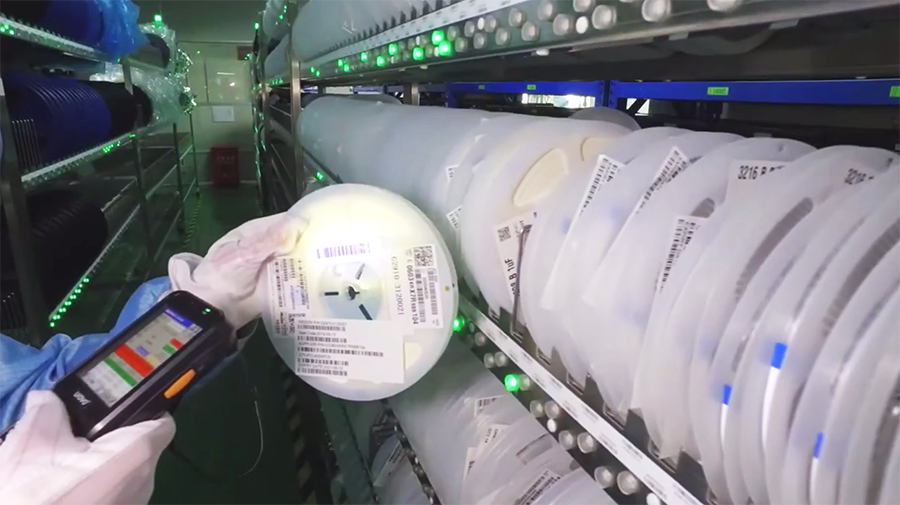
- Inventory Management: Barcodes are used to track and manage inventory levels of raw materials, such as copper-clad laminates, solder masks, and substrates, electronic components, ensuring that there are sufficient materials for production.
- Quality Control: Barcodes are associated with each manufactured PCB. During quality control inspections, the barcode is scanned to access specifications, assembly instructions, and testing requirements.
- Traceability: Barcodes provide traceability for each PCB, allowing manufacturers to monitor the production process, identify potential issues, and track the progress of individual boards.
- Configuration Control: In PCBA production for complex devices, barcodes may be used to ensure that each assembly is configured correctly according to customer specifications.
- Shipping and Delivery: Barcodes are scanned when PCBs are packaged and prepared for shipment, ensuring that the correct products are sent to customers.
You can see barcodes serve as a reliable means of data entry, reducing errors associated with manual data input. They also enable real-time tracking, data recording, and reporting, making it easier for manufacturers to maintain quality standards, track progress, and unleash efficiency.
二、The benefits to use barcode in PCB production:
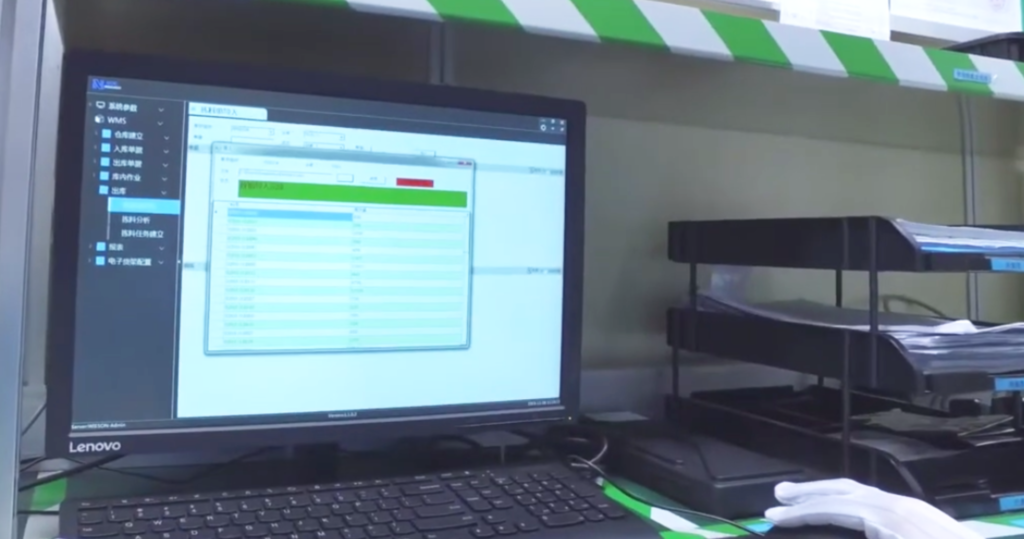
From the functionality of barcodes in PCB production, we can tell barcodes are a critical tool in the modern electronics manufacturing industry, helping manufacturers meet customer requirements and quality standards efficiently. Here are the detailed benefits of using barcode in PCB production:
- Efficiency:
- Streamlined Data Entry: Barcodes eliminate the need for manual data entry, reducing the risk of human errors and saving time.
- Faster Processes: Scanning barcodes is significantly faster than manual data input, leading to increased production efficiency.
- Accuracy:
- Error Reduction: Barcodes virtually eliminate data entry errors, ensuring that the right components are used, and production steps are carried out correctly.
- Quality Assurance: Barcodes help maintain high-quality standards by ensuring that the correct materials and components are used in PCB assembly.
- Traceability:
- Real-time Tracking: Barcodes provide real-time tracking of PCBs throughout the production process, allowing for quick identification of their current status.
- Historical Data: Barcode systems store historical data, making it easier to trace issues, identify trends, and improve processes over time.
- Inventory Management:
- Accurate Inventory Tracking: Barcodes are used to track inventory levels of components, ensuring that there are no shortages or excess materials.
- Cost Savings: Effective inventory management helps reduce carrying costs and minimize waste.
- Quality Control:
- Improved QC Processes: Barcodes are linked to quality control (QC) checklists and specifications, ensuring that each PCB undergoes the required inspections.
- Documentation: Barcodes help generate detailed QC reports, documenting the results of inspections and tests for compliance purposes.
- Reduced Downtime and Errors:
- Minimized Downtime: Quick barcode scans reduce downtime associated with manual data entry, keeping production lines running smoothly.
- Error Prevention: Barcode systems include validation checks, preventing assembly errors and reducing the likelihood of rework.
- Enhanced Reporting and Analytics:
- Data Analysis: The data collected from barcode scans can be used for performance analysis, process optimization, and continuous improvement efforts.
- Decision Support: Access to real-time and historical data allows for data-driven decision-making.
- Cost Savings:
- Labor Savings: Reduced manual data entry and decreased error rates save on labor costs.
- Rework Reduction: Fewer errors mean less rework, minimizing material waste and labor expenses.
- Compliance and Auditing:
- Compliance Assurance: Barcodes help ensure that PCBs are manufactured in accordance with industry standards and customer specifications.
- Auditing Support: Detailed barcode records assist in compliance audits and quality certifications.
Reading Barcode in PCB Production:
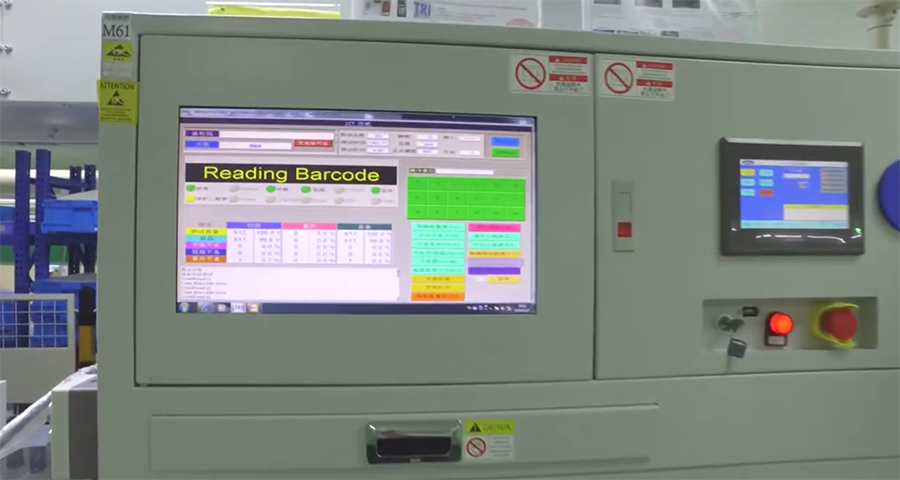
Barcodes play a central role in modern PCB manufacturing by enhancing accuracy, efficiency, and overall productivity. And barcoding technology has become an integral part of supply chain management and quality assurance in the manufacturing industry. To use barcode in PCB manufacturing, factories need to read barcode during production. And there are also some difficulties of Reading barcodes in the PCB production process.
一、The working principle of reading barcodes:
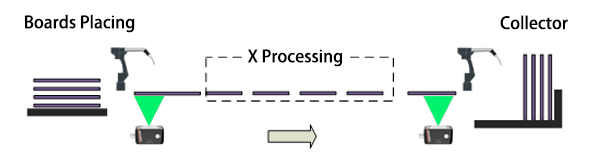
- Install an industrial camera on the PCB assembly line, positioned directly above the circuit board to capture the 2D barcodes when the single or double-row circuit boards pass through.
- The industrial camera captures images of the 2D barcodes upon receiving signals from sensors and proceeds to compare the information contained in the barcodes.
- After collecting the 2D barcode data using a wireless scanning gun, the data is transmitted to a controller via Bluetooth for further processing.
- When the system detects a missing or unreadable 2D barcode for the first time, it triggers an audio and visual alarm and sends a reject signal, recording the incident as “NG” (non-good). If three consecutive instances of missing or unreadable 2D barcodes occur, the system initiates an alarm and issues a stop signal, halting the production line.
- The 2D barcode information collected by the wireless scanning gun and the industrial camera needs to be uploaded to the customer’s backend system.
- After the system comes to a halt, manual intervention is required to reset it, and only then can it resume operation.
二、The difficulties of reading barcodes in the PCB production process:
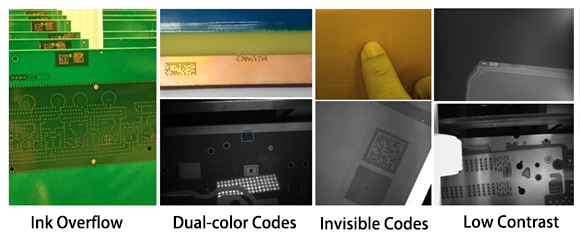
- Complex Manufacturing Processes: PCB production typically involves dozens of steps, each with different requirements for code readers in terms of field of view, setup space, lighting, and more.
- Challenging Barcodes: Common challenging barcodes include those with blocked holes, ink overflow, dual-color codes, low contrast, and more.
- Variations in Material Types: Different batches of products for the same process may have variations in material or color, leading to inconsistent image quality captured by code readers, which can affect recognition.
- Special Functional Requirements: As production lines continue to evolve, there are industry-specific functional requirements placed on code readers.
三、SuperPCBA solutions to difficulties of reading barcodes.
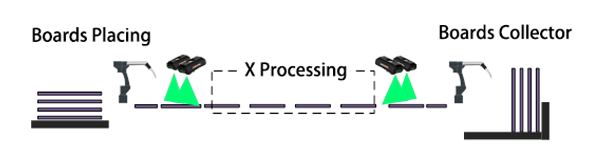
SuperPCBA places great emphasis on the role of Reading Barcodes in the PCB production and assembly process.
- To ensure accurate barcode reading throughout the production process, SuperPCBA selects suitable barcode reader models for different manufacturing stages.
- These readers are equipped with deep learning decoding algorithms to achieve stable and reliable recognition results.
- The barcode reading equipment is designed to automatically switch to optimal parameters using multi-parameter polling functionality.
- Additionally, it has the capability to determine whether a PCB has passed inspection, assess the orientation of the PCB when it passes successfully, and analyze Noread images offline.
Overall, the use of barcodes in PCB production plays a crucial role, enhancing operational efficiency, quality control, and traceability. That’s why SuperPCBA places significant importance on the application of barcodes in the production process. In turn, leads to improved product quality and increased customer satisfaction while simultaneously reducing production costs.
SuperPCBA adheres to a production philosophy of “Quality First” and aims to provide an enhanced collaborative experience for both new and existing customers. We welcome inquiries and discussions from all customers, old and new.