What is control boards? What’s the composition of control board costs?
A control board, also known as a circuit board or PCB (Printed Circuit Board), is a vital component in electronic devices that provides the necessary connections and circuitry to control and manage the functions of the device. It contains various electronic components like microcontrollers, sensors, connectors, and other elements that enable the device to perform specific tasks.
The composition of the cost of a control board can vary based on several factors:
- Components: The cost of electronic components, such as microcontrollers, sensors, capacitors, resistors, connectors, and integrated circuits, forms a significant portion of the total cost.
- Manufacturing: Costs related to the manufacturing process, including fabrication, assembly, soldering, testing, and quality control, contribute to the overall cost.
- Design Complexity: The complexity of the circuit design, including the number of layers in the PCB, the density of components, and the intricacy of routing, can influence the cost.
- Labor: Labor costs for assembling and testing the board play a role, especially if intricate manual labor is involved.
- Materials: The type and quality of materials used in the PCB, such as the substrate material and solder mask, can affect costs.
- Technology: Advanced technologies like multilayer PCBs, high-frequency circuitry, and fine-pitch components may increase costs.
- Quantities: Economies of scale come into play; producing a larger quantity of boards can reduce the cost per unit.
- Special Features: Additional features like custom heatsinks, shielding, and specialized coatings can add to the cost.
Is it important to optimize Control Board Cost?
Optimizing control board cost is important for several reasons:
- Competitive Pricing: A lower cost allows you to offer competitive pricing for your product, attracting more customers.
- Profit Margin: Lower manufacturing costs can lead to higher profit margins per unit sold.
- Market Penetration: If your product’s price is more attractive due to cost optimization, it might gain quicker acceptance in the market.
- Mass Production: Reduced costs enable more economical mass production, which is crucial for scaling up production.
- Cost-Efficiency: Identifying ways to reduce costs can make your production process more efficient, saving resources in the long run.
- Budget Control: Cost optimization ensures that you stay within your budget during the manufacturing phase.
However, while optimizing control board cost is essential, it should not compromise the quality, functionality, and reliability of the final product. Striking a balance between cost reduction and maintaining product quality is key to the long-term success of your electronic device in the market.
Case Study: Analyzing Optimization Methods for Overcrowded Soldering Points in Control Board Design
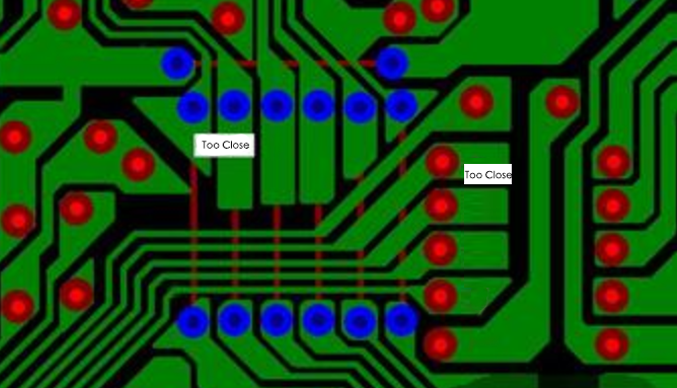
Analysis: In this case, the control board has a relatively high number of plug-in components, resulting in a relatively dense layout. Due to the close proximity of soldering points, with distances ranging from 0.3mm to 0.5mm, there is a risk of solder bridging, particularly exacerbated by poor-quality flux, which can lead to substantial leakage during the rainy season.
Countermeasures: To address this issue, it’s recommended to increase the spacing between soldering points and introduce a layer of solder mask between them. Additionally, strict control over the quality of the flux used is essential to prevent leakage.
Considerations: When designing densely populated PCBs, it’s advisable to maintain a reasonable level of density while allowing for necessary spacing. For instance, even though the minimum recommended spacing might be 0.3mm, if a section of the PCB allows for 0.6mm spacing, it’s recommended to utilize this larger spacing to minimize the probability of issues arising.
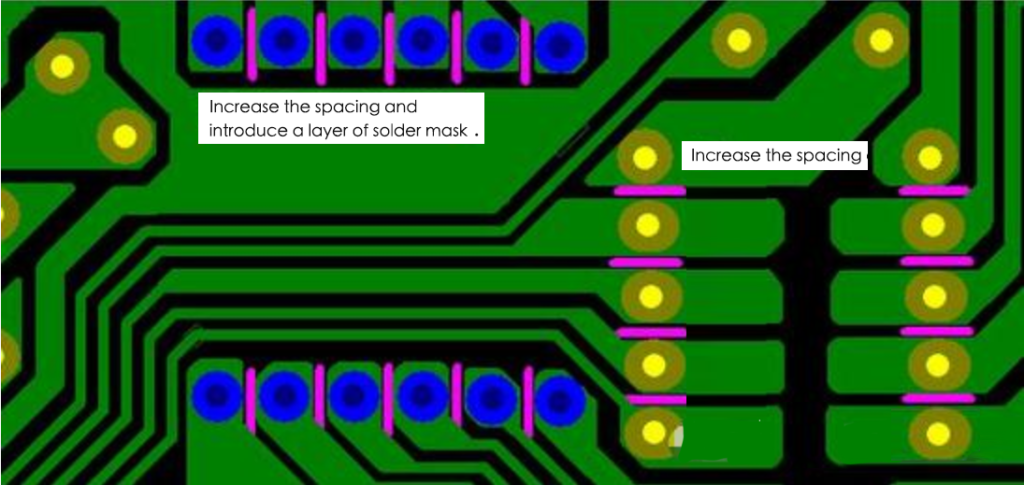
Conclusion: Optimization in design is crucial as it effectively ensures the safety and quality of the circuit board, thereby improving its overall cost-effectiveness. By adopting measures such as adjusting soldering point spacing and using quality flux, we can both enhance the safety of the circuit board and elevate its overall quality, leading to better performance and reliability.
Then how to optimize control board cost?
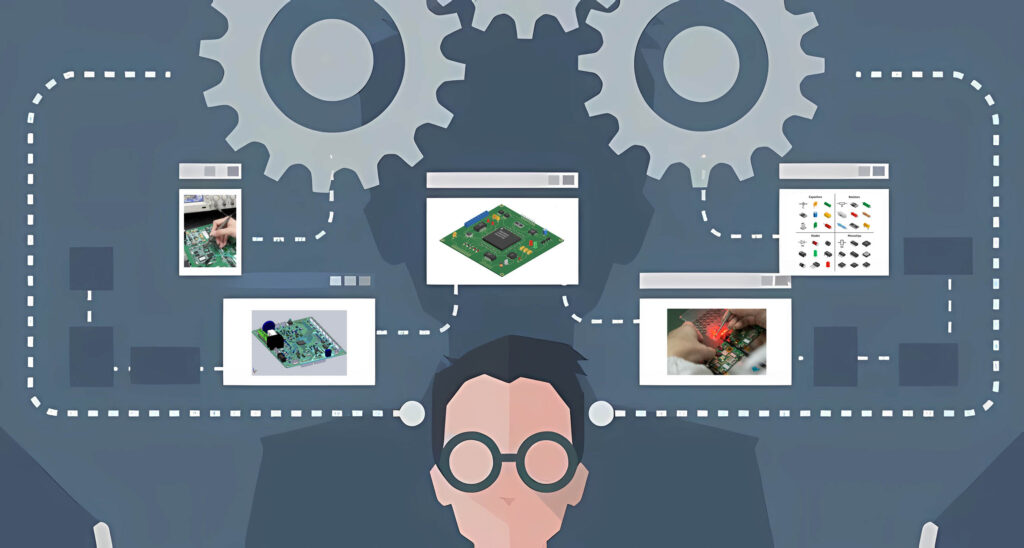
Here are some strategies to optimize control board cost without compromising the quality and functionality of your electronic device:
- Component Selection: Choose components with competitive prices while maintaining quality and performance. Consider alternate sources for components to find the best price.
- Simplify Design: Reduce unnecessary features and complexity in the circuit design. Use standard components and avoid custom or specialized parts unless absolutely necessary.
- Design Efficiency: Optimize PCB layout to minimize board size and routing complexity. Utilize multilayer PCBs effectively to reduce interference and space usage.
- Economies of Scale: Produce larger batches to take advantage of bulk purchasing discounts. Negotiate with suppliers based on higher order quantities.
- Value Engineering: Collaborate with design engineers to find more cost-effective alternatives to components and processes. Focus on functional improvements that can lead to cost savings.
- Distributed Manufacturing: Consider manufacturing in regions with lower production costs while maintaining quality standards.
- Consolidate Components: Replace multiple discrete components with integrated ones where feasible. Combine functions to reduce the number of components.
- Use Standardized Platforms: Utilize development platforms with pre-designed circuitry to save design time and costs.
- Test and Quality Control: Implement stringent testing and quality control to reduce rework and wastage. Identify and address defects early in the manufacturing process.
- Energy Efficiency: Design the circuit for optimal energy consumption to reduce operating costs over time.
- Supplier Relationships: Maintain strong relationships with suppliers to negotiate better pricing and terms. Explore opportunities for collaboration and shared cost savings.
- Continuous Improvement: Regularly review and analyze the manufacturing process for potential improvements. Seek feedback from your team and suppliers on ways to reduce costs.
- Environmental Considerations: Ensure compliance with environmental regulations to avoid fines and penalties.
- Lifecycle Analysis: Consider the total lifecycle cost of the product, including maintenance and disposal costs, when making design decisions.
Consider the total lifecycle cost of the product, including maintenance and disposal costs, when making design decisions. Remember, the goal is not just to reduce costs but to do so while maintaining the quality, reliability, and performance of the final product. Regularly assessing your strategies and making adjustments as needed will help you achieve a well-balanced approach to cost optimization.
What we should pay attention to during we optimize control board costs to avoid decreasing the quality, reliability, and performance of the final control board product?
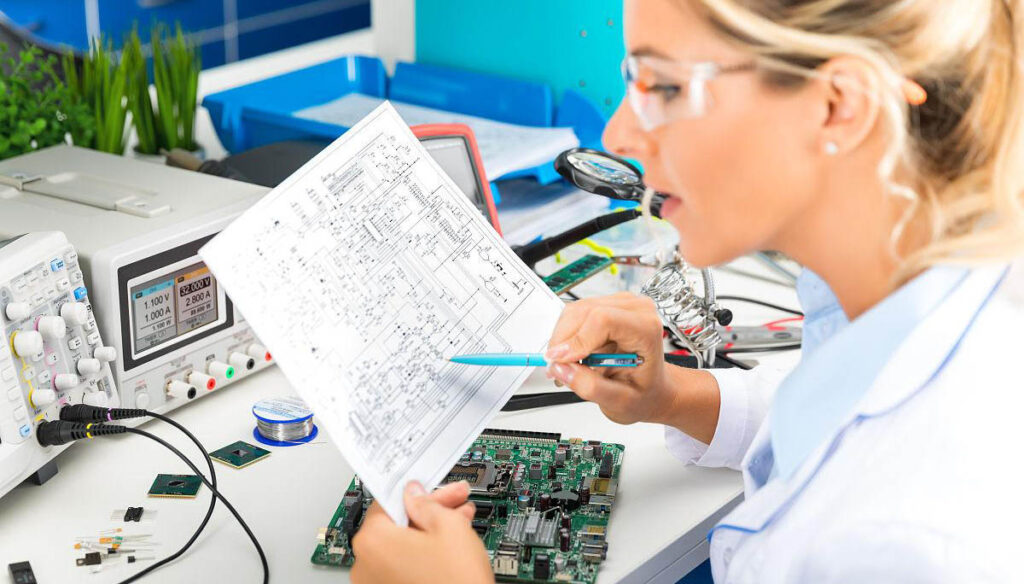
When optimizing control board costs, it’s crucial to ensure that the quality, reliability, and performance of the final product are not compromised. Here are some key points to pay attention to:
- Component Quality: Ensure that cost reduction measures do not lead to the use of low-quality or counterfeit components. Always prioritize components from reputable sources.
- Functional Integrity: Avoid removing critical components or features that directly impact the functionality of the control board. Maintain the essential components required for the control board’s intended purpose.
- Testing and Validation: Rigorous testing and validation are essential. Do not compromise on the testing process to cut costs.Thoroughly verify that the control board meets performance and reliability standards.
- Environmental Considerations: Ensure compliance with environmental regulations and industry standards even while reducing costs.Cutting corners on environmental requirements can lead to legal and reputational issues.
- Temperature and Reliability: Ensure that the control board design can handle the required temperature ranges without compromising its reliability. Use components rated for the appropriate temperature range.
- EMI and Noise Mitigation: Maintain proper EMI shielding and noise filtering components to prevent interference that can affect performance and reliability.
- Power Management: Optimize power management circuits without compromising the stability and efficiency of the board’s power supply.
- Safety and Compliance: Ensure that the control board adheres to safety standards and regulations relevant to its application. Cutting corners on safety measures can lead to hazardous situations.
- Robust Design: Design the board to handle potential stress factors, such as voltage spikes or mechanical vibrations, to prevent premature failure.
- Material Selection: Carefully evaluate alternative materials to ensure they meet quality and reliability standards. Low-cost materials might not have the durability required for long-term use.
- Supplier Relationships: Maintain open communication with suppliers and ensure they understand your quality requirements even as cost reductions are pursued.
- Documentation: Keep comprehensive documentation of the control board’s design, components, and changes made during cost optimization.This documentation is crucial for troubleshooting and future improvements.
- Long-Term Considerations: Keep in mind the product’s lifecycle and consider how cost-cutting measures might impact maintenance and repairs down the line.
- Expertise and Experience: Involve experienced engineers and professionals in the cost optimization process to ensure critical aspects aren’t overlooked.
Conclusion:
Balancing cost optimization with quality, reliability, and performance requires a thoughtful approach and close collaboration between design, engineering, and manufacturing teams. Regular testing, validation, and adherence to industry standards are paramount to delivering a control board that not only costs less but also meets the highest quality standards.