PCB Soldering Definition
The soldering process is an essential step in the PCB assembly process, where electronic components are attached to the PCB using solder. The soldering process involves melting the solder, which is usually made of a mixture of tin and lead, to create a permanent bond between the component leads and the PCB pads.
PCB Soldering Methods
There are two main methods of soldering used in PCB assembly:
1 Wave Soldering

Wave soldering is a common method used in the mass production of printed circuit board assemblies (PCBAs) for through-hole components. The process involves the following steps:
- Flux application: The first step is to apply flux to the through-holes and component leads. This is done to remove any oxidation on the metal surfaces, which can prevent proper solder adhesion.
- Preheating: The PCB is then preheated to the required temperature to activate the flux and prepare the surface for soldering.
- Solder application: Molten solder is then pumped from a heated reservoir through a nozzle or a series of nozzles that create a wave of solder. The PCB is passed over the wave of solder, which wets the exposed metal surfaces and forms a solid solder joint.
- Cooling: The PCB is then cooled to solidify the solder joints.
In addition to these basic steps, there are several variables that must be carefully controlled during the wave soldering process to ensure consistent, high-quality solder joints. These variables include the temperature and flow rate of the solder, the preheat temperature and time, the speed and angle of the PCB as it passes over the solder wave, and the design of the solder mask and through-hole plating. Skilled operators and careful process control are essential for successful wave soldering.
2 Reflow Soldering
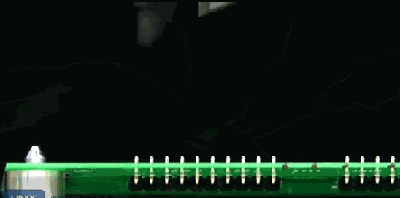
Reflow soldering is a process of melting solder paste to join the components and the circuit board. Here are the detailed steps of reflow soldering:
- Solder Paste Printing: Solder paste is printed onto the pads of the circuit board using a stencil. The stencil is aligned with the board and the paste is applied through the openings in the stencil onto the board.
- Component Placement: The components are placed on the solder paste using a pick and place machine. The machine uses a vacuum nozzle to pick up the components and place them on the pads.
- Preheating: The board is heated slowly to avoid thermal shock to the components. The temperature is raised to a level where the moisture in the paste can evaporate, typically around 150-200°C.
- Reflow: The board is heated rapidly to a temperature where the solder paste melts and reflows, typically around 220-250°C. The solder joints are formed as the molten solder cools.
- Cooling: The board is cooled gradually to avoid thermal shock to the components. The temperature is reduced to below the melting point of the solder, typically around 100°C.
- Inspection: The board is inspected to ensure that all the components are soldered correctly and there are no defects.
Reflow soldering is widely used in the PCB assembly process due to its accuracy and reliability.

During the soldering process of PCB assembly, there are several things that should be paid attention to:
- Temperature control: The temperature of the soldering iron and the reflow oven should be carefully controlled to avoid overheating or underheating the components, which can result in poor soldering quality or damage to the components.
- Soldering time: The soldering time should be appropriate to ensure that the solder melts and flows evenly, but not too long to avoid damaging the components due to overheating.
- Solder paste application: The amount of solder paste applied to the pads should be appropriate, as too much or too little can cause poor soldering quality.
- Component placement: The components should be placed accurately and securely on the pads to ensure proper contact and alignment during the soldering process.
- Flux application: The flux should be applied to the pads and components to remove any oxide layers, which can interfere with the soldering process and affect the quality of the joint.
- Inspection: The soldering joints should be inspected after the process to ensure that they are properly formed, have good wetting and bonding, and are free of defects such as voids or cracks.
By paying attention to these factors during the soldering process, the quality and reliability of the PCB assembly can be improved.